Could Solid-State Batteries Dominate the Battery Landscape?
Whitepaper
Published: August 10, 2023

The changing energy storage landscape is looking to alternative battery designs to meet the critical requirements for a rapidly expanding electric battery market.
All solid-state batteries (ASSBs) present an opportunity to rise beyond the energy densities of traditional battery systems and mitigate manufacturing costs. However, developers still need to overcome unique developmental challenges to dominate the battery landscape.
This whitepaper highlights the analytical technologies and techniques used for component development to support ASSBs' meteoric breakthrough.
Download this whitepaper to learn more about:
- The future of ASSBs in the electric battery market
- How to overcome cell breathing issues and cell dimensional changes
- Scalability challenges and considerations to support ASSB development
Introduction
All solid-state battery (ASSB) technology, defined as having only solid components, will unlock
materials chemistry limitations from traditional battery technologies and enable alternative
activities and advanced designs. The costs of battery manufacturing are trending down, and
energy density is trending up, however, this trend is plateauing. This plateau in energy density
and cost efficiency offers a perfect opportunity for new battery innovations and ASSBs stand
to be the primary battery system of the future.1
The primary difference between ASSB and lithium-ion battery (LIB) technology is the utilization of
a solid electrolyte, which presents its own development challenges. ASSBs will need to overcome
unique challenges including market penetration and R&D obstacles. The solid electrolyte
interface between the cathode and anode materials generate a variety of electrochemical and
mechanical considerations that will require innovative analytical technologies.
The potential of ASSBs to revolutionize the battery industry is resulting in new battery
designs and material configuration solutions such as wider electrochemical windows,
enhanced ionic conduction, SEI engineering, boosting mechanical properties, anode-less
designs, and optimized thermal management innovations. The ASSB market will require
the proper analytical testing technology to support these solutions and maintain the pace
of development necessary to break into the battery market. Additionally, we are seeing the
global push for wide-spread electric battery adoption for a variety of industries. Countries
leading ASSB development are positioning themselves to reap the immense benefits, both
economic and environmental, of the green revolution.
In this whitepaper, we will look at the factors that need to be overcome by ASSB developers
in order to dominant the battery landscape, as well as the newest ASSBs designs, innovations
and analytical equipment considerations to support ASSBs' meteoric breakthrough into the
battery landscape.
WHITE
PAPER
The Meteoric Rise of Solid-State Batteries:
Innovations and Analytical Instrument Breakthroughs
Shattering the Energy Density Ceiling with Solid-State Batteries: Innovations and Analytical Instrument Breakthroughs
www.perkinelmer.com 2
Factors Driving the Electric Battery Market
As global temperatures continue to rise, campaigns to reduce
our collective CO2 footprint, such as Net Zero initiatives, are
some of the primary mechanisms driving the demand for
the electric battery market. Nations around the world are
recognizing the need for a more sustainable future and electric
battery systems are primed to be the cornerstone technology
in this green revolution. NetZero initiatives are pushing for
100% of car and 50% of heavy truck sales to be electric by
2035. Additional goals include electrifying buildings, cleaning
up the energy grid and investing heavily in green electrical
generation.2-5
Key Supply Chain Considerations for Solid State Batteries
¡ Raw Material Acquisition
¡ Processing Strategy
¡ Scale Up
Solid State Batteries Market and Applications
The changing energy storage landscape is looking to alternative
battery designs to reach the critical requirements needed for a
rapidly expanding electric battery market. Of these new battery
designs, ASSBs are positioned as one of the most promising
developments in the market. Estimated commercial product
release of ASSBs is projected for 2023 but will require several
optimizations in order to meet this benchmark.6 The main
requirements needed for the solid state battery (SSB) market
to reach its full potential include:
¡ High energy density, High Wh/Kg and Wh/L and large
capacity potential
¡ Fast charging capabilities
¡ Wide temperature ranges and tolerance
¡ Constant volume with limited compression
¡ Cycle stability
¡ Safe and nonflammable
¡ Scalability
¡ Sustainability
The patenting activity in Europe and China are increasing,
however, the patent landscape is primarily dominated by
Japanese companies from all supply chain levels. For the
cathode active materials market, Korea, China, and Japan make
up the majority of the top market leaders.8
On July 7, Japan’s
Nihon Keizai Shimbun surveyed patent filings related to all
solid-state batteries in 10 countries including the US and Europe.
The survey found Toyota was the leader in patent registrations
from 2000 to March 2022, reaching 1,331 patent registrations.
Panasonic Holdings ranked second with 445 registrations and
Idemitsu Kosan ranked number third with 272 registrations. In
total, Asian markets dominant in patent landscape with six of
the top ten leading corporations in patent registrations being
Japanese companies, while the remaining four are Korean.9
Benefits of ASSBs
Traditional battery designs, such as LIBs, are still demonstrating
optimized performance but are starting to plateau in the areas
of energy density and cost of manufacturing. ASSBs will enable
battery manufacturers to rise beyond energy densities of
traditional battery systems and potentially mitigate manufacturing
costs with the following projected and observed benefits.
Improved Energy Density
ASSBs offers the potential of high energy densities due largely to
its stability at high voltages. At the cell level, engineers can replace
graphite with Li-metal and increase cell size. At the pack level,
engineers can implement higher volume utilization removing the
need for cooling and reducing battery failure.10
Improved Working Temperature
ASSBs will utilize solid electrolytes that are less flammable
(~200 °C) and tolerate higher temps (80-150 °C). This will allow
manufacturers to design systems without cooling and battery
management systems components, such as cooling subsystems,
exhaust ducts, and blowers.11 Additionally, researchers have
established ASSBs can operate within favorable thermal
parameters: -40 °C workability, 25 °C high-power, and 100°C
cycling.12, 13 Currently, ASSBs cannot match the same level power
as LIBs but should be able to function at higher temperatures,
thus improving safety and performance.
medical technologies smart card
Wearables and E-Textiles
Internet of Things (IoT) applications RFID
Transport and
logistical applications
SENSORS PORTABLE ELECTRONICS
Large scale energy storage
medical technologies smart card
Wearables and E-Textiles
Internet of Things (IoT) applications RFID
Transport and
logistical applications
SENSORS PORTABLE ELECTRONICS
Large scale energy storage
medical technologies smart card
Wearables and E-Textiles
Internet of Things (IoT) applications RFID
Transport and
logistical applications
SENSORS PORTABLE ELECTRONICS
Large scale energy storage
Portable Electronics
Transport and Logistical Applications
Large Scale Energy Storage
The Primary Applications of SSB Technologies Include:7
medical technologies smart card
Wearables and E-Textiles
Internet of Things (IoT) applications RFID
Transport and
logistical applications
SENSORS PORTABLE ELECTRONICS
Large scale energy storage
medical technologies smart card
Wearables and E-Textiles
Internet of Things (IoT) applications RFID
Transport and
logistical applications
SENSORS PORTABLE ELECTRONICS
Large scale energy storage
medical technologies smart card
Wearables and E-Textiles
Internet of Things (IoT) applications RFID
Transport and
logistical applications
SENSORS PORTABLE ELECTRONICS
Large scale energy storage
Internet of Things (IoT) Applications
Medical Technologies
Smart Cards
medical technologies smart card
Wearables and E-Textiles
Internet of Things (IoT) applications RFID
Transport and
logistical applications
SENSORS PORTABLE ELECTRONICS
Large scale energy storage
medical technologies smart card
Wearables and E-Textiles
Internet of Things (IoT) applications RFID
Transport and
logistical applications
SENSORS PORTABLE ELECTRONICS
Large scale energy storage
medical technologies smart card
Wearables and E-Textiles
Internet of Things (IoT) applications RFID
Transport and
logistical applications
SENSORS PORTABLE ELECTRONICS
Large scale energy storage
RFID
Sensors
Wearables and E-Textiles
Shattering the Energy Density Ceiling with Solid-State Batteries: Innovations and Analytical Instrument Breakthroughs
www.perkinelmer.com 3
Improved Fast Charging
Fast charging capability, especially for electric vehicles, is crucial
for ASSB market penetration. ASSBs maintain better efficiency and
stability at high temperature for the cell level, which translates to
a no step-profile at the pack level. This key feature of ASSBs was
established by researchers at QuantumScape and demonstrated
the following ASSB fast charging capabilities.14
For 4C charging:
¡ 0 - 80% charge in 15 minutes
¡ 10 - 80% charge in 12 minutes
¡ And maintained repeated 4C charge cycle life to 400 cycles
Safety
Increased projected safety due to the removal/reduction of
flammable liquid electrolytes, thus reducing the need for certain
safety measures such as a heat shield and crash zones.
Improved Abuse Conditions
ASSBs have also demonstrated improved abuse tolerances and
thermal abuse.15, 16 Key abuse tolerances that are optimized with
ASSBs include overcharge protection, mechanical robustness,
overheating protection and short-circuit protection.
System Simplicity and Improved Engineering Efficiency
The optimized energy density and improved working temperatures
of ASSBs eliminate the need for redundant cell voltage sensing and
reduce (if not remove) the need for a cooling system. Additionally,
this will allow ASSB designs to simplify the thermal management
system, lowering cost of manufacturing.
Reduce Battery Pack Size and Weight
Due to the potential higher energy density and power density, ASSB
designs have the potential to decrease the size of the battery pack
by as much as 20% and reduce the weight by as much as 25%. This
would enable high energy throughput with controlled weight and size
optimizations, producing higher range electric vehicles and batteries
with more power and energy density.17
Cost and Supply Chain Issues
As mentioned in the previous section, the potential for ASSB
technology to revolutionize the battery industry is there, but in order
for developers to drive the supply of materials needed to build out
the ASSB industry researchers will need to demonstrate ASSBs are
not just a theoretical player but can meet the market requirements
and appeal to investors.
Perhaps, one of the greatest challenges in the coming years will
be as the demand for battery energy systems rapidly expands,
companies involved in the electric battery industry will be racing to
keep up with this demand.18 This will only exacerbate the existing
issue of raw material prices.19 Raw material quality needs to be
clearly defined and the appropriate supply chain for ASSB raw
materials have not been established.
Global Response to Battery Supply Chain Development
In the global battery market, South Korea, Japan, China, and
Germany continue to position themselves as industry leaders in
innovation and development. As a result, many other countries
have expressed their intent to secure domestically-controlled supply
chains. Of global importance, is the United States government has
expressed its intent to secure critical minerals for the battery industry
and recognizes the importance of this industry as a core pillar of
economic competitiveness, national security, and sustainability. The
United States has stated several strategic elements to catch up and
eventually lead in battery innovation and development.20
These strategies include:
Implement legislation to support and foster the demand of
battery-based technologies
Applying supply chain initiatives to support increasing demand
of battery-based technologies, such as electric vehicles
With the implementation of supply chains and domestic
manufacturing, the United States is hoping to catalyze the auto
industry’s transition into electrification
According to the National Blueprint for Lithium Batteries, thereare
five goals for the battery industry stratum set fourth by the United
Sates that are designed to enable long-term U.S. economic
competitiveness and job creation, the ability to reach decarbonization
goals, and meet national security requirements.20
These five goals are outlined below:
1. Secure access to raw and refined materials and support
the discovery of alternate sources of critical minerals for
commercial and defense applications.
2. Promote the growth of a U.S materials-processing base that is
capable of meeting domestic battery manufacturing demand.
3. Stimulate the U.S electrode, cell and pack manufacturing sectors.
4. Support U.S. critical materials recycling at scale and a full
competitive value chain.
5. Continue to advance U.S. battery technology leadership
via strong support of scientific R&D, STEM education and
workforce development.
Similar initiatives are underway around the world, such as the
action plan from the European Battery Alliance led by the European
Commision, which aims to enable 90% of the Union's demand for
batteries to be met with domestically made products by 2030.21
It is evident that the U.S. battery industry is playing catch up, but the
aggressive government and private industry initiatives driving the
security of raw materials, reinforcing supply chain, and advancing
scientific leadership, indicates a dramatic shift necessary for battery
development in the United States.20
Shattering the Energy Density Ceiling with Solid-State Batteries: Innovations and Analytical Instrument Breakthroughs
www.perkinelmer.com 4
Scalability Considerations to Support
ASSB Development
The four factors that need to be considered for adequate
scalability of ASSBs are supply chains, materials properties,
processing costs and the battery ecosystem. Analytical
technologies enhance several key drivers with regards to
these four factors, specifically material acquisition and
processing, process rate and process yield. In addition to
proper analytical support, scalability of ASSBs will be heavily
influenced by key outcomes such as scaled technology
performance and reproducibility.22
Scale Up Challenges
Upscaling to large cell designs will present issues that lead to
delays, these scale up challenges include:
Finding the right material suppliers at scale
Difficulties in regulatory approval for production facilities or
product launch
Development of new and different manufacturing
processes for ASSB catholytes and electrolytes
Higher complexity in material handling, production processes
and production steps may lead to increased product costs.
Dependent on type of solid electrolyte, new additives, doping
or coatings, materials costs could have a significant impact on
total cell costs. Exacerbating scale up challenges further is the
availability of sustainable resources, equipment, and talent in
this sector.
Fast Charging Obstacles
Fast charging capability is perhaps one of the most attractive
features for ASSBs and is critical to its market penetration
potential. Currently, the major obstacles fast charging ASSB
development must face is:23
¡ Sluggish Electrochemistry
¡ High Hysteresis
¡ Internal Temperature Rise
¡ Accelerated Aging
¡ Useful Capacity Losses
Safety Considerations
Comprehensive testing of ASSBs will be required to validate its
largely theoretical safety benefits. However, there have been
several noteworthy developments evaluating thermal properties
and crush comparisons to conventional LIB systems.
Crush Testing Comparisons
Crush Comparisons were performed with ASSB cell designs
against conventional LIB pouch cell configurations in an
automotive battery module. Findings demonstrated higher
peak force could be achieved with ASSBs and event-free
intrusion in x and y directions were significantly higher for
ASSBs. Thus, ASSBs could enable future designs to load
modules with higher intrusion and mechanical forces.
This may lead to higher overall safety standards, cost
mitigation, simplification in design, higher energy capacity
and better range, and optimized volume utilization.
24
Thermal Evaluation Comparisons
Potential temperature rise increases significantly with energy
density and must be a critical consideration for future ASSBs.
Considering temperature rise as a metric of safety, researchers
should rely on thermal modeling studies to assess safety
using thermogravimetry analysis (TGA), differential scanning
calorimetry (DSC), and thermomechanical analyzer (TMA).
Key Safety Testing Technologies
TGA and DSC
¡ Thermal characterization to identify and characterize
binders and solid electrolytes
TMA
¡ Measure thermal and mechanical properties
TGA
¡ Thermal stability and decomposition profile
¡ Battery failure analysis
Pressure Considerations, Cell Dimensional
Changes and Cell Breathing
The potential of a battery systems to produce varying
degrees of pressure over its lifetime plays a crucial role in
its marketability. Low pressures are considered desirable
for battery systems as the cell pressure is transferred to the
module and pack frame. Large forces, derived from these
pressures, can lead to deformation to the battery frame and
battery failure. Engineers can address higher pressures with
heavier frames but will add significant weight and decreased
performance on products like electric vehicles.
Traditional liquid battery configurations can generate high
amounts of pressure due to the swelling of electrodes and gas
generation. The design of ASSBs will help mitigate this pressure
concern as they do not have the same swelling and gas
generation issues as traditional liquid batteries.
Shattering the Energy Density Ceiling with Solid-State Batteries: Innovations and Analytical Instrument Breakthroughs
www.perkinelmer.com 5
To ensure the integrity of the battery system over a lifetime, low
volume changes as well as pressures are required. Traditional
LIBs are vulnerable to cell dimensional changes during charging
and discharging, where one electrode is expanding while the
other is contracting. Depending on the materials used, a battery
cell can be exposed to significant degrees of expansion.
For instance, when Lithium alloys with silicon in the anode
the volume changes are significantly greater. The volume
changes can cause decreased functionality at the particle level,
electrode, and SEI layer. Volumetric changes can be greater
when utilizing lithium metal anodes as their cycling produces
dendrites formation.25, 26
The effects of cell dimensional changes include:
¡ Diminished energy density
¡ Reduced Cycle Life
¡ Increase in Impedance
¡ Safety Concerns
Therefore, cell dimensional changes should be a top priority
for manufacturers. Pressure can improve performance of
lithium metal cycling and the variation in lithium foils perform
differently under varying pressures. Lithium foils all perform
differently with variations in capacity fade, dimensional
changes and electrolyte sensitivity.25, 26
The main variations in lithium foils include:
¡ Thickness, where thinner is typically optimal
¡ Deposition method
¡ Coatings and pre-treatment of the lithium
¡ Underlying composition as seen in doped lithium and
lithium alloys. Commonly doped and alloyed elements
are In, Sn, Zn, Si, Al, Ag, and Mg. Potential benefits of
utilizing doping and alloying elements include better
capacity retention
Compressive Loads and Requirements
The majority of the current ASSB designs require loads 5 - 200x
that of Li-ion batteries.This dramatic increase in compressive
load requirements will add to the cost of manufacturing and
increase the volume and weight of the system. There is an
urgent need, and opportunity, for solutions to cell breathing and
volume expansion issues for ASSBs.25, 26
Solutions to Cell Breathing
1. Compression Pads and Spring Elements
Compression elements will need to be designed for long
term compression at elevated temperatures.
2. Thin Ceramic Electrolytes
The nonflammable and low-cost ceramic electrolytes
provide a thin and electrolyte material for a separator with
a porous scaffold.
3. Lithium Metal Anode
Lithium plating within porous scaffold for high rate and low
resistance at room temperature, without compression or
external expansion
4. Cathode-Flexible Platform
Compatible with existing and next generation cathodes
that will further enhance energy density and power
Our understanding of cell dimensional changes is still not
complete and there is an urgent need for research to map out
the effects and develop a greater understanding.25, 26
Solid-State Electrolytes
Removing the liquid electrolyte causes several unique design
challenges such as interfacial resistance and voids. As Li-ions are
transported during cycling, electrochemical interactions between
battery components will result in the formation of dendrites and
voids. Solid electrolytes require the malleability to fill in small voids
and porosities while maintaining the ionic conductivity required to
be better than liquid electrolytes.27
There are many types of ASSB electrolytes, all with varying
properties and considerations. Each electrolyte is analyzed
based on its mechanical properties, ion conductivity, anodic and
cathodic stability, electronic and ionic low area-specific resistance
(ASR), stability (thermal, chemical, oxidation, reduction), and
processability. Depending on the configuration of the ASSB, each
type may offer a unique benefit to the manufacturer. It is based
on this uniqueness of each electrolyte, that manufacturers must
carefully assess which type is optimal for their own applications.
ASSB electrolytes include:
Polymers
Polymers are scalable and stable electrolytes with good
electrochemical properties and one of the easiest electrolytes to
process into cells. They are also compliant, enabling compact
arrangements to address cell dimensional changes during
cycling. Polymers have already established their functionality in
EV applications. However, their mechanical properties are not as
good as oxide and sulfide electrolytes with28
Shattering the Energy Density Ceiling with Solid-State Batteries: Innovations and Analytical Instrument Breakthroughs
www.perkinelmer.com 6
Oxides
Oxides are air stable electrolytes with good mechanical and
electrochemical properties. However, they are challenging to
scale up, lack flexibility, and often have compatibility issues.28
Sulfides
Sulfides are scalable, slightly flexible, and have good mechanical
and electrochemical properties. However, they are unstable in
air and have combability issues to account for.28
Halides
Halides possess desirable properties such as high ionic
conductivity, high oxidation voltage and good stability toward
oxide cathode materials. However, there are still challenges in
scalability, stability, and achieving high humidity tolerance.28
Ceramic
The company QuantumScape is currently in development
of a solid-state ceramic electrolyte, tens of micrometers in
thickness, that also doubles as the separator. The solid ceramic
is designed to suppress the formation of dendrites while
enabling lithium ions to pass back and forth.32
Key Analytical Testing Technologies Include:
ICP-MS and ICP-OES
¡ Analyze electrolyte for elemental and compound
impurities (ppb and ppt range)
GC-MS and LC-MS
¡ Analyze solvent composition
¡ Identify volatile semivoliatile and chemical compound
impurities
¡ For compositional and purity/impurity analyses
¡ Content in electrolytic solution
Hyphenation
¡ Hyphenation combines two or more technologies to
answer what gases evolved and when
¡ TG-MS, TG-MS, TG-GC/MS
ASSB Cathodes
ASSB cathodes provide the positive ion sources, such as
lithium ions, in the ASSB battery. Common materials used in
cathodes include:
¡ NMC (NCM) – Lithium Nickel Cobalt Manganese Oxide
(LiNiCoMnO2)
¡ LFP – Lithium Iron Phosphate (LiFePO4)
¡ LNMO – Lithium Nickel Manganese Spinal (LiNi0.5Mn1.5O4)
¡ NCA – Lithium Nickel Cobalt Aluminum Oxide (LiNiCoAlO2)
¡ LMO – Lithium Manganese Oxide (LiMn2O4)
¡ LCO – Lithium Cobalt Oxide (LiCoO2)
Analytical techniques are necessary to analyze some of the raw
metals using the manufacturing of battery cathodes and impurity
detection in R&D and QA/QC. This ensures high quality of the
cathode materials and optimized battery performance.28
LIBs utilize nickel rich cathode materials that have oxygen
problems, especially at higher temps where we see thermal
events. In many ASSBs, cathode materials will be similar, so the
risk in ASSBs will still be applicable.28
Transitional Metal Oxide (FePO4)
FePO4 is an inexpensive, earth-abundant cathode material
that can provided with a domestic supply chain. It is also less
expensive and safer than many of the cathode materials but
provides a lower energy density.30
High Nickel and Cobalt Free Cathode Active Material
Utilizing high nickel and Cobalt-free cathodes can provide higher
voltages and energy densities. However, to find the right match
of materials surface properties and pore properties much be
tailored together.30
ASSB Cathode Analytical Testing Technologies and Considerations
ICP-MS
¡ High sensitivity for quantifying impurities in anodic and
cathodic materials
¡ Battery failure analysis (cathode materials)
ICP-OES
¡ Impurities and elemental analysis
¡ Characterize and develop anodic and cathodic materials
TGA and Hyphenation
¡ Battery failure analysis- used to look at what happens to
any battery components during failure
ASSB Anodes
The ASSB anode provides the negative ion sources in the ASSB
battery. Graphite is one of the primary anode materials utilized
in many battery systems, due to its ability to reversibly place
lithium ions between its layers. Fully charged batteries position
Li-ions between the graphite sheets, then during discharging,
electrons move from the anode to the cathode. The negatively
charged cathode is then stabilized by the Li-ions migrating from
in between the graphite sheets of the anode to the cathode.
ASSB batteries, like LIBs, can be made up of graphite, a binder,
and a conductive addictive that is coated on copper foil.
Anode materials should demonstrate optimized porosity and
conductivity, durability, low cost and a voltage that is matched
with the desired cathode. Methods that ensure material quality
rely on ICP-MS to analyze impurities and hyphenated technologies
to detect molecules absorbed to the surface of the electrodes.29
Shattering the Energy Density Ceiling with Solid-State Batteries: Innovations and Analytical Instrument Breakthroughs
www.perkinelmer.com 7
ASSB Anode Variations
There are several ASSB anode configurations that are
being developed, three of those variations include ASSB
graphite-silicon anodes, ASSB lithium-metal anodes, and
ASSB anode-free configurations.
ASSB Graphite-Silicon Anode
The addition of silicon to conventional graphite anodes
provide greater battery capacities and energy densities.
However, silicon becomes problematic as it expands to
nearly a factor of 4 after repeated cycling. The solution to
this silicon-graphite expansion issue is instead of utilizing
a large piece of silicon, you replace it with nanoparticles
of silicon. Nano-silicon materials can limit cracking due to
differences in surface area to volume ratio.
Pure Lithium Metal Anode
Silicon-graphite anodes, although offer better energy density
than pure graphite, are nowhere near the energy densities
provided by pure lithium metal anodes. Lithium metal anodes
have been around for a long time in liquid battery systems but
are notoriously difficult to develop. While they offer greater
capacity and energy density, they are subject to dendrite
growth across the electrolyte.31
It was proposed that solid-state technology offers a potential
way to block dendritic growth and capture the true potential
of pure lithium metal anodes. However, dendrite growth is
persistent and if the solid electrolyte is polycrystalline and has
grain boundaries, then dendrites will grow through the grain
boundaries and short out the battery. There are two solutions
currently in development to solve this dendritic growth issue
for pure lithium metal anode applications.31
Dendritic growth solutions include:
¡ Utilizing a glassy solid-state electrolyte, with no
grain boundaries
¡ Utilizing a Ceramic electrolyte that has a low ionic conductivity
Anode-Free ASSBs
The company QuantumScape is implementing an anode free
ASSB application that instead of utilizing a graphite anode to store
lithium ions, their anode free design utilizes an electrical contact in
leu of the anode. The ceramic electrolyte provides a high dendritic
resistance and the lithium metal anode enables high-rate cycling.
The cathode contains the lithium ions that during battery charging
the lithium ions migrate through the separator and form a flat,
dendrite-free layer between the electrical contact and separator.
This application has the potential to reduce the weight and cost of
the battery significantly.32
Separators
The ASSB separator divides the anode from the cathode, forming
an isolator for electrons and allowing the migration of ions.
Traditional battery separators are porous polymer membranes
are saturated by a liquid electrolyte. Separators for ASSBs, do
not require liquid saturation and, in many cases, utilize the solid
electrolyte itself as the separator.29 30
ASSB Anode Analytical Testing Technologies and Considerations
ICP-MS
¡ High sensitivity for quantifying impurities in anodic and
cathodic materials
ICP-OES
¡ Impurities and elemental analysis
¡ Characterize and develop anodic and cathodic materials
ASSB Separator Analytical Testing Technologies and Considerations
IR
¡ Identify and characterize advanced materials used for
separators, cell housings and pack enclosures
TGA and DSC
¡ Thermal characterization
Separator performance (melting point, crystallinity,
thickness, chemical composition, porosity)
Analytical Technologies for Thermal and
Mechanical Properties
Thermal and mechanical properties offer key insights
into battery performance and safety and are critical in the
manufacturing process. These insights are gained from
analyzing properties such as crystallinity, melting point,
thermal stability, and decomposition profiles.29
Oxygen at the cathode becomes a key risk for ASSBs, for
example in lithium continuing batteries that utilize nickel rich
cathode material there is the potential for oxygen derived
issues, especially at higher temperatures where thermal events
occur. Therefore, it is critical that manufacturers include robust
instrumentation, such as a DSC, to monitor thermal conditions.
Shattering the Energy Density Ceiling with Solid-State Batteries: Innovations and Analytical Instrument Breakthroughs
www.perkinelmer.com 8
Recycling of All Solid-State Batteries
With nearly 11 million tons of previously used LIBs estimated
to exist by 2030, ASSBs will no doubt reflect a similar volume
of waste after its adoption. Currently, the motivating drivers
of recycle LIBs include mitigating raw material acquisition and
optimizing supply chain, reducing the negative environmental
consequences of battery development, and ensuring the battery
industry maintains a healthy impact on society and vulnerable
groups. ASSBs, with demands for similar raw materials, are already
being designed with recyclability as a key process in its lifecycle.33
The recycling process of ASSBs will begin with deactivating and
shredding of the old battery modules. After removing electrolyte
residues, hydrometallurgical and pyrometallurgical procedures
need to be carried out to recover materials like lithium and
cobalt. The characterization of ASSB materials using elemental
analysis and cell chemistry are also critical to ensure effective
recycling efficiencies.34, 35
ASSB recycling will rely on a collection of physical processes
and analytical methods to provide the information necessary
to begin the initial assessment of the recycling scrap. Thus,
analytical testing equipment will play a fundamental role in both
the characterization of the re-synthesized recycled ASSBs and
the crucial reduction in the environmental and social impact of
ASSB development.35
Key Analytical Technologies to Consider for Thermal
and Mechanical Property Analysis Include:
TGA and DSC
¡ Thermal characterization to identify and
characterize binders
TMA
¡ Measure thermal and mechanical properties
TGA
¡ Thermal stability and decomposition profile
¡ Battery failure analysis
Key Analytical Testing Technologies Include:
ICP-MS and ICP-OES
¡ Determination of all elements of interest
AA, TXRF, EDX
¡ Composition of recycled scrap materials
IC
¡ Characterize anionic components of scrap metal
GC, GC-MS, LC, LC-MS
¡ Identify original used electrolyte components and
information about additives
IR
¡ Identification and advanced material characterization
TGA and DSC (Thermal gravimetric analysis (TGA)
and differential scanning calorimetry (DSC)
¡ Investigate mixture of anode and cathode materials
(black mass)
Hyphenation
¡ Greater insights by combining two or more techniques,
enabling reverse engineering and a better understanding
of evolved gases. i.e. TGIR, TG-MS, TG-GC-MS
The Future of All Solid-State Batteries
2023 marks the projected role out of ASSBs into the
energy market and presents an incredible opportunity for
manufacturers to break through the energy density plateau.
As this technology begins to mature, the opportunities to
implement ASSBs in applications like medical devices, sensors
and electric vehicles will significantly increase demand.
Thus, ASSB manufacturers will need to prepare for this
anticipated demand by securing raw materials, reinforcing
supply chains and utilize key analytical technologies to optimize
battery development.
Shattering the Energy Density Ceiling with Solid-State Batteries: Innovations and Analytical Instrument Breakthroughs
www.perkinelmer.com 9
References by Section
1. 2021 New Economy Forum. Bloomberg New Economy,
www.bloombergneweconomy.com/nef2021/. Accessed 13
Dec. 2022.
2. Meyer, Robinson. “The Rise of Greenflation.” The Atlantic, 2
Feb. 2022, www.theatlantic.com/science/archive/2022/02/
greenflation-prices-inflation-climate-change-coffeelumber/621456/.
3. Burchfiled, Shifting cultivation geographies in the Central and
Eastern US, EnvironResLeft 17, 054049 (2022)
4. Accenture Sustainability. Accenture, www.accenture.com.
Accessed 13 Dec. 2022.
5. CORPORATION, TOYOTA MOTOR. “Sustainability.” Toyota
Motor Corporation Official Global Website, global.toyota/en/
sustainability/?padid=ag478_from_header.
6. EU, Maxell. “Maxell to Mass Produce World’s First Small
Sized Sulfide Based All Solid State Battery in 2023.” Maxell, 19
Aug. 2022, www.maxell.eu/News/maxell-to-mass-produceworlds-first-small-sized-sulfide-based-all-solid-state-battery-in2023/#:~:text=Maxell%20Europe%20Ltd%20are%20proud.
7. Avicenne Energy Slides. “Solid-State Battery Summit.”
BigMarker.com, www.bigmarker.com/cambridgeinnovation-institu1/Solid-State-Battery-Summit-Day1?bmid=1a98e445fcd6&.
8. Morgan Advanced Materials Slides. “Solid-State Battery
Summit.” BigMarker.com, www.bigmarker.com/
cambridge-innovation-institu1/Solid-State-Battery-SummitDay-1?bmid=1a98e445fcd6&.
9. Nikkei 2022 Advanced Materials Slides. “Solid-State Battery
Summit.” BigMarker.com, www.bigmarker.com/cambridgeinnovation-institu1/Solid-State-Battery-Summit-Day1?bmid=1a98e445fcd6&.
10. BMW Group Slides. “Solid-State Battery Summit.” BigMarker.
com, www.bigmarker.com/cambridge-innovation-institu1/
Solid-State-Battery-Summit-Day-1?bmid=1a98e445fcd6&.
11. Toyota Slides. “Solid-State Battery Summit.” BigMarker.com,
www.bigmarker.com/cambridge-innovation-institu1/SolidState-Battery-Summit-Day-1?bmid=1a98e445fcd6&.
12. Journal of the electrochemical society. 2017. 164, A6254.
13. Kato, Y., Hori, S., Saito, T. et al. High-power all-solid-state
batteries using sulfide superionic conductors. Nat Energy 1,
16030 (2016). https://doi.org/10.1038/nenergy.2016.30.
14. QuantumScope Slides. “Solid-State Battery Summit.”
BigMarker.com, www.bigmarker.com/cambridgeinnovation-institu1/Solid-State-Battery-Summit-Day1?bmid=1a98e445fcd6&.
15. Sci. Ad., DOI: 10.1126/sciadv.abl839
16. ACS Appl. Mater. Interfaces, 2017, 9, 1507
17. Stellantis Slides. “Solid-State Battery Summit.” BigMarker.com,
www.bigmarker.com/cambridge-innovation-institu1/SolidState-Battery-Summit-Day-1?bmid=1a98e445fcd6&.
18. Boston Consulting Group Slides. “Solid-State Battery
Summit.” BigMarker.com, www.bigmarker.com/cambridgeinnovation-institu1/Solid-State-Battery-Summit-Day1?bmid=1a98e445fcd6&.
19. Mauler, Lukas, et al. “Technological Innovation vs. Tightening
Raw Material Markets: Falling Battery Costs Put at Risk.”
Energy Advances, 24 Jan. 2022, pubs.rsc.org/en/content/
articlelanding/2022/ya/d1ya00052g#, 10.1039/D1YA00052G.
20. “National Blueprint for Lithium Batteries.” Energy.gov,
www.energy.gov/eere/vehicles/articles/national-blueprintlithium-batteries.
21. Colthorpe, A. (2022, April 6). European action plan to
accelerate growth of battery value chain. Energy Storage
News. https://www.energy-storage.news/european-actionplan-to-accelerate-growth-of-battery-value-chain/.
22. Huang, Kevin J., et al. “Manufacturing Scalability Implications
of Materials Choice in Inorganic Solid-State Batteries.”
Joule, vol. 5, no. 3, Mar. 2021, pp. 564–580, 10.1016/j.
joule.2020.12.001. Accessed 15 June 2021.
23. Stellantis Slides. “Solid-State Battery Summit.” BigMarker.com,
www.bigmarker.com/cambridge-innovation-institu1/SolidState-Battery-Summit-Day-1?bmid=1a98e445fcd6&.
24. Mercedes-Benz Slides. “Solid-State Battery Summit.”
BigMarker.com, www.bigmarker.com/cambridgeinnovation-institu1/Solid-State-Battery-Summit-Day1?bmid=1a98e445fcd6&.
25. BMW Slides. “Solid-State Battery Summit.” BigMarker.com,
www.bigmarker.com/cambridge-innovation-institu1/SolidState-Battery-Summit-Day-1?bmid=1a98e445fcd6&.
26. Stellantis Slides. “Solid-State Battery Summit.” BigMarker.com,
www.bigmarker.com/cambridge-innovation-institu1/SolidState-Battery-Summit-Day-1?bmid=1a98e445fcd6&.
PerkinElmer, Inc.
940 Winter Street
Waltham, MA 02451 USA
P: (800) 762-4000 or
(+1) 203-925-4602
www.perkinelmer.com
Shattering the Energy Density Ceiling with Solid-State Batteries: Innovations and Analytical Instrument Breakthroughs
For more information visit www.perkinelmer.com
For a complete listing of our global offices, visit www.perkinelmer.com/ContactUs
Copyright ©2023, PerkinElmer, Inc. All rights reserved. PerkinElmer® is a registered trademark of PerkinElmer, Inc. All other trademarks are the property of their respective owners.
908351 PKI
27. Banerjee A, Wang X, Fang C, Wu EA, Meng YS. Interfaces
and Interphases in All-Solid-State Batteries with Inorganic
Solid Electrolytes. Chem Rev. 2020 Jul 22;120(14):6878-
6933. doi: 10.1021/acs.chemrev.0c00101. Epub 2020
Jun 30. PMID: 32603100.Tutorial: J. Janek, “Solid-State
Batteries-Solid Electrolytes, Electrode Interfaces, and Full
Cells” 2022 AABC Europe.
28. X. Li, J. Liang, X. Yang, K. Adair, C. Wang, F. Zhao, X.
Sun. Progress and Perspectives of Halide-based Lithium
Conductors for All-Solid-State Batteries. Energy Environ.
Sci., 13, 1429-1461 (2020).
29. Battery Analysis Guide. Edition 1. Cathode Analysis.
https://pki.showpad.biz/webapp2/content/channels/
ad1090a5ba40efa8371b8625f5573852/.
30. Scott, Alex. “Lithium-ion’s Solid Opportunity.” Chemical &
Engineering News, 17 Sept. 2021, cen.acs.org/energy/energystorage-/solid-opportunity-lithium-ion-batteries/99/i32.
31. JCESR Slides. “Solid-State Battery Summit.” BigMarker.com,
www.bigmarker.com/cambridge-innovation-institu1/SolidState-Battery-Summit-Day-1?bmid=1a98e445fcd6&.
32. “An Anode-Free Battery Future?” Batterytechonline.com,
4 Feb. 2021, www.batterytechonline.com/industry-outlook/
anode-free-battery-future. Accessed 25 Sept. 2022.
33. Low-Temperature Molten-Salt-Assisted Recovery of Valuable
Metals from Spent Lithium-Ion Batteries. ACS Sustainable
Chem. Eng. 2019, 7, 19, 16144– 16150. August 26, 2019.
https://doi.org/10.1021/acssuschemeng.9b03054.
34. Luqman, Azhari, Sungyool, Bong, Xiaotu, Ma, Yan Wang.
Recycling for All Solid-State Lithium-Ion Batteries. Matter,
Volume 3, Issue 6. 2020. https://doi.org/10.1016/j.
matt.2020.10.027.
35. The Analytical Needs for Recycling Lithium-Ion
Batteries. Nowak, Sascha. Lab Manager. July 19, 2021.
https://www.labmanager.com/big-picture/lithium-ionbatteryproduction/the-analytical-needs-for-recycling-lithiumionbatteries-26231.
Brought to you by
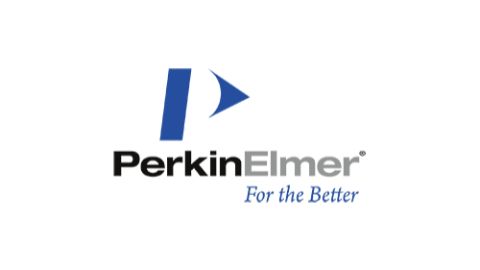
Access This Whitepaper for FREE Now!
Information you provide will be shared with the sponsors for this content. Technology Networks or its sponsors may contact you to offer you content or products based on your interest in this topic. You may opt-out at any time.