What Does Sustainability Accreditation Really Mean for Scientific Companies?
ACT label scheme takes a deep look into the life cycle of lab products to allow scientists to make more informed choices
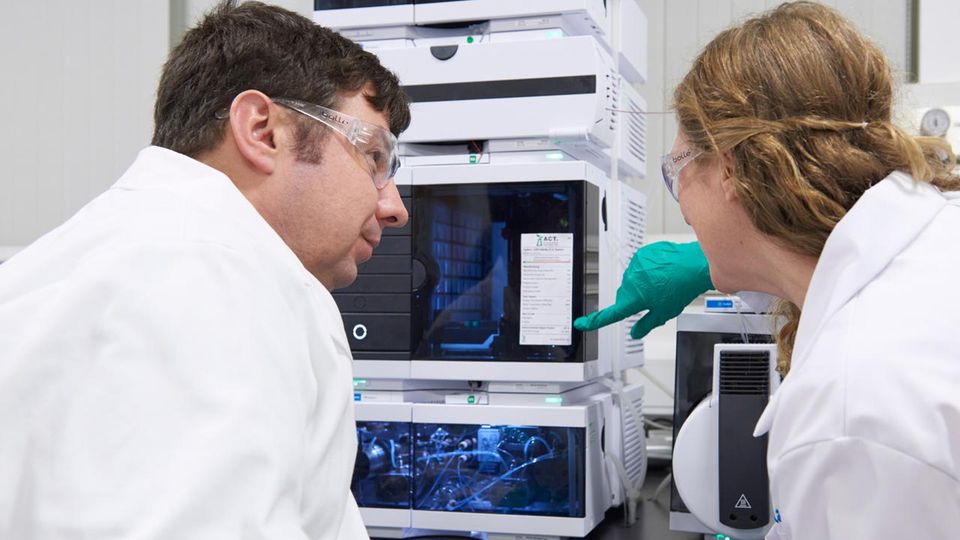
Complete the form below to unlock access to ALL audio articles.
The emphasis on the importance of sustainability in our lives is becoming ever more prominent, and that’s something that extends to the workplace. While we can all make simple choices, like whether to print an email or not, or using a reusable water bottle rather than disposable cups, making environmentally friendly and sustainable choices in a laboratory environment can be a little more tricky.
At the same time, there’s ever-increasing priority given to and legislation from Universities, Institutes and laboratories across the sectors on ensuring scientists make choices of equipment, consumables and services that help them meet their green goals. Consequently, it’s important that the companies and manufacturers that supply them are able to demonstrate their green credentials and enable consumers to make informed decisions. That might sound simple, but in practice there are many aspects that must be considered, not just whether something is made from recycled plastic or how many miles it has been transported.
My Green Lab, a not-for-profit organization focused on lab sustainability, established its Accountability, Consistency, and Transparency (ACT) label scheme to help do just this. But what does this entail and why are companies adopting it?
We spoke to Dr. Michael Frank, associate vice president global marketing, liquid phase separations division, Agilent Technologies, to find out what ACT accreditation means for a company and why he thinks schemes like this are so important.
Karen Steward (KS): When and how did you first become aware of My Green Lab’s ACT label scheme and what motivated you to promote its adoption at Agilent?
Michael Frank (MF): The former CEO of My Green Lab approached Agilent's CTO in the fall of 2019 to introduce the idea and concept of My Green Lab as an organization, as well as their programs such as the ACT labels. Coincidentally, I was at our Santa Clara headquarters at the same time and was able to attend this meeting. I was immediately excited about the ACT label program, as I had been looking for several years for such an independent program to document and share the efforts that Agilent and, specifically, the high-performance liquid chromatography (HPLC) division I represent have made over the years to improve our environmental footprint and that of our products.
Agilent has long been committed to implementing sustainable practices throughout its operations, and organizations such as Barron’s, Forbes and Dow Jones have ranked Agilent among the most sustainable companies in the life sciences industry, but how can we highlight this to our customers?
After discussions with the senior executive team at Agilent, we decided this was exactly the right initiative to help Agilent to showcase our efforts in environmental sustainability, and we joined as a sponsor in 2020.
KS: What is the reality for a company when they decide to go for My Green Lab ACT accreditation on an instrument or product? What steps are involved?
MF: It is important to note that the product audit is performed by an independent subcontractor, and not by My Green Lab themselves to avoid any conflict of interest. Typically, the ACT label audit begins with a meeting between the manufacturer's representative and the auditor to explain the nature and use of the product and to determine whether any ACT label categories may not be appropriate for the product in question. Then details regarding required documentation or energy consumption methodology are clarified. And then the long internal process begins to gather all the required documentation. The great thing about ACT labels is that they provide a holistic view of a product's (and manufacturing site's) environmental impact, but the downside for the manufacturer is that a huge amount of information must be gathered across many organizations within a company. To give just a few examples: ISO certifications from corporate headquarters, information on renewable energy use or waste production from facility management colleagues, product lifecycle data from research and development, packaging take-back certificates from many different countries, the weight of electronics, plastic and metal components from manufacturing - and much, much more!
KS: How long does it typically take for accreditation to be obtained and are there cost implications for those involved?
MF: For a new product to be ACT labeled, it can take several months to collect all the data - it also depends on whether a company is new to ACT labeling and all the colleagues who need to contribute to it need to be identified first, or whether a corresponding process is already established. The recertifications, which are due every two years, are then much faster. As for the cost implications - yes, there are fees associated with the ACT label to cover the work of the audit firm that has to review all the documentation - and of course there is also a cost associated with the work required of the manufacturer to collect all the data. But as you can see from the ever-growing number of ACT labels at Agilent, we clearly see the value in these investments.
KS: It seems like a lot of work to attain accreditation, why do you think it is worthwhile?
MF: Judging by the growing number of companies signing up to My Green Lab's ACT label program, we, at Agilent, are not the only ones who think it's worth investing in. On the other hand, customers are already starting to make ACT labels a requirement, or at least prefer such products. The reason for this is surely the fact that the ACT label gives a clear indication of a product's environmental footprint in a truly holistic way, not just an energy consumption value and, most importantly, issued from an independent organization.
KS: Do you foresee a time when green accreditation systems like the ACT label will be standard or even mandatory?
MF: I am not sure if the overall market size of the laboratory market - compared to consumer markets - is large enough for regulators to create specific legislation on this topic, but we see that more and more customers are demanding clear and transparent information on the environmental footprint of products for laboratories. In addition, there are already regulations on how "green" labeling should be done that are either in place or under discussion, such as the European "Environmental Claims Directive" or the Federal Trade Commission's "Guidelines for the Use of Environmental Marketing Claims", which could prohibit any kind of self-certification in the future, even in B2B business. Finally, I am pleased that My Green Lab's programs have already been recognized by the United Nations (UN) and serve as the key indicator of performance for the biotech and pharma sectors in the UN's Race to Zero initiative, in which thousands of companies worldwide are already participating.
KS: What’s next for Agilent and My Green Lab?
MF: While our work on getting our instruments and supplies ACT labeled continues, we were very proud to be the first sponsor of the My Green Lab Certification program, which is considered the international gold standard for laboratory sustainability best practices. Agilent is working to ensure its own demonstration laboratories globally are My Green Lab Certified, already having achieved the highest level “Green” certification for Agilent labs in Waldbronn, Germany; Cheadle, UK and Santa Clara, US sites.
Dr. Michael Frank was speaking to Dr. Karen Steward, Senior Science Writer for Technology Networks.
About the interviewee
Dr. Michael Frank joined Agilent in 2005 and has held different positions in the pharmaceutical segment marketing as well as in the liquid phase separations division. He was appointed to his current role as associate vice president of global marketing of the liquid phase separation business in mid-2013, being responsible for the product management and marketing of Agilent’s liquid chromatography, capillary electrophoresis and dissolution products.
Prior to Agilent, Dr. Frank was the director of analytics at Graffinity Pharmaceuticals, after a merger renamed to Santhera Pharmaceuticals (SIX: SANN) with headquarters in Basel, Switzerland, where he was responsible for high-throughput chemical library analysis and the analytical operations for medicinal chemistry support.
Born in Cape Town, South Africa, but raised in Germany, Dr. Frank studied at the University of Heidelberg, Germany, and at the Strathclyde University Glasgow, Scotland, and holds a PhD in Chemistry. His PhD work was performed at the Max-Plank-Institute-for-Medical-Research in Heidelberg with Prof. Heinz A. Staab on synthesizing porphyrin-cyclophanes as model-systems for the photosynthesis process. During that time, he became very familiar with a multitude of analytical and spectroscopic tools, like LC, GC, MS and NMR.